
Big End Cap Locating Tubes |
These are not necessary for the construction of this engine, I have added them, as I prefer the caps to be accurately located.
The locating tubes are made from stock thin walled brass tube.
The internal diameter of the tube, is a sliding fit on the location bolts.
The holes for the location tubes are drilled from the cap end, right through the cap and part way into the big end forging.
The locating tubes are held in place in the bearing cap, using Loctite or similar.

|
Big End Cap Locating Tubes |
This image shows the locating tubes, fastened into place and ready for the con rod, big end to be bolted together.

|

Con Rod With Fitted Big end Locating Tubes |
 |

Turning the Big End Faces |
Turning the Big End Faces
The Con Rod is bolted onto a suitably sized rod, and the face is skimmed down, each side, evenly until the width is correct.
The Con Rod can be used in this state, but I prefer to skim the face further, leaving a protruding end boss, each side, as it looks better.

|

Turning the Big End Spigot |
Forming the Big End Spigot
The Dial Clock Indicator shown, is used to provide an easy to use and accurate depth stop.
Makes it easier to cut the spigot, as you can see how far the slide is moving.
The procedure can be done by eye or by fixing a suitable stop on the slide.
I turned the faces down till they blend or meet up with the arm of the con-rod.
Making sure that the cuts are even each side, dimensions are not critical, for this operation.
I used a round ended parting tool to skim the face down to the spigot, as it gives a nice curve to the finished article.

|

Measuring Width |
Here I'm measuring the width of the big end, to ensure that I take equal curs from both sides.
I'm using a cheap digital caliper, these are surprisingly accurate, if used carefully, just try not to get them wet or oily.
Again the dimensions are more cosmetic that critical.

|

Turning the Big End Faces |
The split between the shells, is obvious in this image, as I had not tightened the bolts, but just slipped the con rod on to the rod, to take the picture.
At least you can see the raised spigot more clearly, also the rounded corner left by the tool.

|

Polishing the Big End Faces
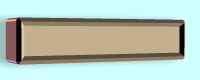
|
Polishing the Big End Faces
You will have gathered by now, that I, do like to get a bit of a polish on my engine parts.
Polishing the parts is not a requirement for the engine to function correctly, and is purely cosmetic.
This is one of my High Tech polishing wheels, made from softwood scrap, and running in the lathe chuck.
Various grades of abrasive are used, using a finer and finer grade till a suitable finish is achieved.
You need to use a different wheel for each grade of abrasive, so that the coarser grades don't contaminate the polish.
Polishing techniques will be covered in a different section.

|